Metal fabrication is an intricate process, a symphony of machinery, manpower, and metal that when performed correctly, results in a finished product of unparalleled quality. However, creating this harmony requires more than just excellent skills and premium equipment, such as those provided by Woodward Fab. It also requires optimal workflow, the lifeblood of any metal fabrication project. This blog post aims to discuss how you can streamline your metal fabrication workflow for maximum efficiency.
Understanding the Metal Fabrication Workflow
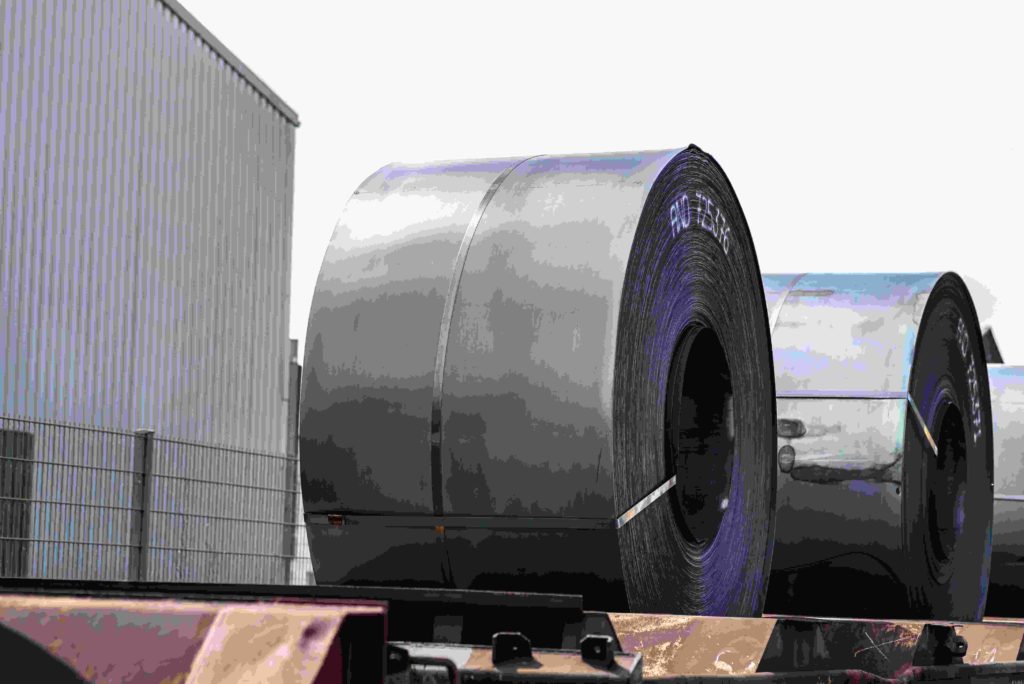
What is the Metal Fabrication Workflow?
Workflow, in the broadest sense, is the orchestrated and repeatable pattern of business activity enabled by the systematic organization of resources. In the context of metal fabrication, it encompasses everything from the initial design and material sourcing to the fabrication and finishing processes. Understanding and optimizing this workflow is key to remaining competitive and profitable in the dynamic metal fabrication industry.
The Role of Workflow in Metal Fabrication
Workflow optimization plays a pivotal role in the success of your metal fabrication projects. Properly managed, it ensures smooth transitions from one phase to the next, reduces downtime, and fosters an environment of continuous improvement. It’s not just about working harder; it’s about working smarter.
Strategies to Optimize Your Metal Fabrication Workflow
Analyzing the Existing Workflow
Before you can improve your workflow, you need to fully understand your current process. This involves an in-depth analysis of each step, taking into account not just the sequence of tasks but also the time taken and resources used at each stage. It’s also crucial to identify any bottlenecks or inefficiencies that may be hindering productivity.
Implementing Lean Manufacturing Principles
Incorporating lean manufacturing principles can significantly streamline your metal fabrication workflow. Derived from the Toyota Production System, lean manufacturing aims to minimize waste and maximize productivity. One popular lean tool is the 5S system (Sort, Set in order, Shine, Standardize, and Sustain), a workplace organization method that uses a list of five Japanese words, all starting with “S”. When properly implemented, these strategies can significantly reduce waste, shorten production time, and contribute to a safer, more productive work environment.
Use of High-Quality Tools and Advanced Equipment
The quality of your equipment plays a significant role in workflow optimization. High-performance tools, such as those provided by Woodward Fab, not only increase accuracy and consistency but also reduce the likelihood of downtime due to equipment malfunction. Moreover, embracing modern technology, like CNC machines and automated systems, can revolutionize your production line and significantly increase throughput.
Employee Training and Skills Development
Your team is the heart of your metalwork operation. Providing them with regular training and opportunities for skills development is an investment that will pay off in increased productivity, improved morale, and a safer working environment. A skilled workforce can leverage their expertise to troubleshoot issues, improve processes, and maintain a high standard of quality.
Improving Key Aspects of Your Metal Fabrication Workflow
Streamlining Design and Prototyping
The use of CAD/CAM software can drastically cut down design and prototyping time. It allows you to catch and correct potential issues early in the design process, saving you valuable time and resources down the line.
Efficient Material Handling and Storage
Proper organization and storage of materials can eliminate unnecessary movement and handling, further streamlining your workflow. Investing in material handling equipment and storage solutions can also increase workspace safety.
Effective Quality Control Measures
Quality control is the guardian of your reputation. Implementing robust QC measures ensures that defects and inconsistencies are caught early before they make it to the final product. This not only maintains your standards but also saves time and resources that would be spent on rework.
Embracing a Culture of Continuous Improvement
Workflow optimization is not a one-time task, but rather an ongoing commitment to excellence and improvement. Encourage feedback from your team, regularly reassess your workflow, and don’t be afraid to make changes. With a proactive approach to improvement and the right tools at your disposal, you can achieve a highly efficient and productive metal fabrication workflow.
Conclusion
Workflow optimization is more than just a strategy; it’s a mindset. From investing in high-quality tools like those from Woodward Fab to promoting a culture of continuous improvement, every element contributes to an optimized and efficient metal fabrication workflow. Remember, the journey towards optimization is ongoing, and every step you take in the right direction is a stride towards increased productivity and success in your metal fabrication projects.
Related Post:
-
Sheet Metal Fabrication Trends 2024: What to Watch For
-
Sheet Metal Bend Radius: The Key to Durability
-
How the Electric Vehicle market is driving changes in sheet metal fabrication technology
-
Small Pipe Bender Innovations: Shaping the Future of Fabrication
-
Sheet Metal Bend Relief Guidelines: Ensuring Successful Fabrication